图书介绍
表面处理技术手册 修订版【2025|PDF下载-Epub版本|mobi电子书|kindle百度云盘下载】
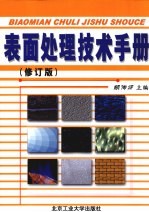
- 胡传炘主编 著
- 出版社: 北京:北京工业大学出版社
- ISBN:9787563919895
- 出版时间:2009
- 标注页数:994页
- 文件大小:60MB
- 文件页数:1015页
- 主题词:金属表面处理-技术手册
PDF下载
下载说明
表面处理技术手册 修订版PDF格式电子书版下载
下载的文件为RAR压缩包。需要使用解压软件进行解压得到PDF格式图书。建议使用BT下载工具Free Download Manager进行下载,简称FDM(免费,没有广告,支持多平台)。本站资源全部打包为BT种子。所以需要使用专业的BT下载软件进行下载。如BitComet qBittorrent uTorrent等BT下载工具。迅雷目前由于本站不是热门资源。不推荐使用!后期资源热门了。安装了迅雷也可以迅雷进行下载!
(文件页数 要大于 标注页数,上中下等多册电子书除外)
注意:本站所有压缩包均有解压码: 点击下载压缩包解压工具
图书目录
第1章 基本知识1
1.1 表面工程及表面处理技术的分类和用途1
1.1.1 什么是表面工程1
1.1.2 表面处理技术分类1
1.1.3 表面技术应用2
1.2 表面涂覆层及处理方法标记符号3
1.2.1 表面涂覆层及处理方法标记符号3
1.2.2 涂覆层表示方法举例5
1.3 金属涂(镀)层基本性能6
1.3.1 结合强度6
1.3.2 孔隙率及密度6
1.3.3 耐蚀性6
1.3.4 硬度6
1.3.5 电阻率6
1.4 金属的腐蚀与防护6
1.4.1 金属腐蚀与腐蚀分类6
1.4.2 腐蚀机理8
1.4.3 电极电位9
1.4.4 电位—pH图12
1.4.5 腐蚀速度13
第2章 基体前处理15
2.1 表面整平15
2.1.1 磨光与抛光15
2.1.2 成批光饰22
2.1.3 其他机械整平方法27
2.2 除油30
2.2.1 有机溶剂除油31
2.2.2 化学除油32
2.2.3 电化学除油37
2.2.4 低温除油39
2.2.5 超声除油40
2.2.6 擦拭除油41
2.2.7 滚筒除油41
2.3 浸蚀42
2.3.1 浸蚀的分类42
2.3.2 常用浸蚀剂的作用42
2.3.3 浸蚀工艺44
2.3.4 弱浸蚀50
2.3.5 超声场内浸蚀51
2.3.6 浸蚀-除油联合处理51
2.3.7 工序间防锈52
2.4 电抛光与化学抛光52
2.4.1 电抛光52
2.4.2 化学抛光60
第3章 电镀65
3.1 电镀基础65
3.1.1 电镀原理65
3.1.2 电镀的结晶过程及影响电镀层结晶粗细的因素65
3.1.3 均镀能力和深镀能力及影响因素67
3.1.4 析氢对电镀过程的影响69
3.1.5 合金电镀70
3.1.6 阳极过程72
3.1.7 金属镀层的基本性能73
3.2 单金属电镀76
3.2.1 镀锌76
3.2.2 镀镉97
3.2.3 镀锡108
3.2.4 镀铜118
3.2.5 镀镍136
3.2.6 镀铬153
3.2.7 镀铅164
3.2.8 镀铁165
3.3 合金电镀172
3.3.1 镀铜合金172
3.3.2 镀锡合金179
3.3.3 镀镍合金183
3.3.4 镀锌合金186
3.3.5 镀多元合金188
3.4 稀贵金属电镀189
3.4.1 镀银190
3.4.2 镀金与金合金192
3.4.3 镀钯与钯镍合金195
3.4.4 其他稀贵金属的电镀196
3.5 特种电镀200
3.5.1 复合电镀200
3.5.2 塑料及其他非金属的电镀207
3.5.3 特种材料上的电镀213
3.5.4 刷镀与局部电镀217
3.5.5 双极性电镀225
3.6 有关电镀的国家标准目录226
第4章 氧化、着色与染色227
4.1 钢铁的氧化227
4.1.1 钢铁氧化的实质227
4.1.2 氧化工艺流程227
4.1.3 溶液配制及工艺条件227
4.1.4 工艺操作中注意事项228
4.1.5 氧化膜常见缺陷及处理228
4.1.6 钢铁氧化应用229
4.2 铜及铜合金的氧化229
4.2.1 铜及铜合金氧化的实质229
4.2.2 氧化工艺流程229
4.2.3 溶液配制及工艺条件229
4.2.4 工艺操作中注意事项230
4.2.5 铜及铜合金氧化应用230
4.3 铜及铜合金的钝化230
4.3.1 钝化工艺流程230
4.3.2 钝化液化学成分及工艺条件230
4.3.3 工艺操作中注意事项231
4.4 铝及铝合金的氧化231
4.4.1 装饰性氧化232
4.4.2 硬质阳极氧化242
4.4.3 特种阳极氧化246
4.5 染色与着色250
4.5.1 着色方法分类及比较250
4.5.2 整体着色法(自然显色法)250
4.5.3 吸附着色法(化学着色法)252
4.5.4 电解着色法257
4.6 封闭处理260
4.6.1 热水封闭260
4.6.2 蒸汽封闭260
4.6.3 金属盐封闭260
4.7 铝及铝合金阳极氧化着色阳极氧化膜耐晒度的人造光加速试验261
第5章 电铸262
5.1 电铸原理、特点及应用262
5.1.1 电铸原理262
5.1.2 电铸特点262
5.1.3 电铸应用262
5.2 电铸芯模设计、类型及材料263
5.2.1 芯模设计263
5.2.2 芯模类型263
5.2.3 芯模材料263
5.3 电铸的前处理264
5.3.1 金属芯模表面剥离膜形成264
5.3.2 非导体芯模表面金属化265
5.4 电铸铜266
5.4.1 硫酸铜电铸266
5.4.2 氟硼酸电铸铜267
5.5 电铸镍268
5.5.1 电铸镍特点及种类268
5.5.2 瓦特型电铸镍269
5.5.3 氨基磺酸型电铸镍271
5.5.4 高速电铸镍273
5.6 电铸铁273
5.6.1 电铸铁特点273
5.6.2 电铸液273
5.7 电铸后处理274
5.7.1 脱模274
5.7.2 加固274
5.8 复合电铸274
5.8.1 概述274
5.8.2 复合电铸工艺275
5.8.3 电铸镍钴合金275
5.8.4 电铸镍锰合金276
5.9 电铸技术的应用278
5.9.1 组合式可溶性象形阳极电铸技术278
5.9.2 精密电极制造技术280
5.9.3 电极精密电铸举例283
5.9.4 选择性电铸技术289
第6章 化学镀292
6.1 化学镀镍292
6.1.1 化学镀镍的原理293
6.1.2 化学镀镍层的性能293
6.1.3 化学镀镍的前处理295
6.1.4 化学镀镍的工艺条件及镀液的配制295
6.1.5 工艺条件和溶液组成对化学镀的影响296
6.1.6 化学镀层的用途298
6.1.7 镀液维护298
6.1.8 其他类型的化学镀镍工艺298
6.1.9 不良镀层的消除300
6.1.10 新技术300
6.2 化学镀铜301
6.2.1 化学镀铜溶液及工艺条件301
6.2.2 化学镀铜溶液中各组分的使用和影响302
6.2.3 化学镀铜溶液的配制、使用和维护303
6.2.4 化学镀铜装置303
6.3 化学镀金304
6.3.1 化学镀金的应用304
6.3.2 化学镀金的工艺304
6.4 化学镀银305
6.4.1 化学镀银的应用305
6.4.2 化学镀银溶液的配方和镀银工艺305
6.5 化学镀钯307
6.5.1 用次磷酸盐作还原剂的溶液成分和镀钯工艺307
6.5.2 用肼作还原剂的化学镀钯工艺308
6.6 化学镀钴308
6.6.1 用次磷酸钠作还原剂的化学镀钴溶液及工艺308
6.6.2 用硼氢化物作还原剂的化学镀钴溶液及工艺310
6.6.3 用二甲氨基硼烷作还原剂的化学镀钴溶液及工艺310
6.7 化学镀的新技术发展310
6.7.1 化学镀铜研究动向310
6.7.2 化学镀镍研究动向311
第7章 化学转换膜处理313
7.1 钢铁的磷化313
7.1.1 磷化原理313
7.1.2 磷化膜组成及性质313
7.1.3 钢铁磷化的用途314
7.1.4 磷化处理分类315
7.1.5 磷化液成分及工艺条件315
7.1.6 磷化工艺317
7.1.7 磷化工艺操作中注意事项317
7.1.8 磷化后处理318
7.1.9 磷化膜质量检验319
7.1.10 磷化液游离酸度及总酸度的测定319
7.2 钢铁的常温发蓝319
7.2.1 发蓝膜层构成320
7.2.2 常温发蓝液成分及工艺条件320
7.3 铝铬酸盐转化处理320
7.3.1 铝铬酸盐转化处理实质320
7.3.2 铬酸盐处理液321
7.3.3 金属的磷酸盐转化膜321
7.4 转化膜试验方法321
7.4.1 金属材料上的转化膜 单位面积膜质量的测定重量法321
7.4.2 锌和镉上铬酸盐转化膜 试验方法321
7.4.3 电镀锌和电镀镉层的铬酸盐转化膜321
7.5 钢铁工件涂装前磷化处理技术条件321
7.6 着色磷化膜322
7.6.1 化学着色工艺322
7.6.2 电化学着色工艺322
7.6.3 应用举例323
7.7 有色金属磷化323
7.7.1 铝及其合金的磷化323
7.7.2 锌及其合金的磷化324
7.7.3 镁合金的磷化324
7.8 磷化渣及处理324
7.8.1 磷化渣生成324
7.8.2 磷化渣组成325
7.8.3 磷化渣控制325
7.8.4 磷化渣处理325
7.8.5 磷化渣综合处理方案326
第8章 热浸镀327
8.1 引言327
8.1.1 热浸镀原理327
8.1.2 热浸镀工艺种类327
8.1.3 热浸镀层的性能及应用328
8.2 热镀锡328
8.2.1 热镀锡原理328
8.2.2 热镀锡工艺329
8.2.3 热浸镀锡钢板性能及应用330
8.2.4 热浸镀锡钢板检验331
8.3 热浸镀锌333
8.3.1 热浸镀锌原理333
8.3.2 热浸镀锌工艺334
8.3.3 热镀锌钢材应用339
8.3.4 热镀锌涂层检测339
8.3.5 热镀锌标准341
8.4 热浸镀铝341
8.4.1 热镀铝原理341
8.4.2 热镀铝工艺342
8.4.3 热镀铝钢材应用344
8.4.4 热镀铝涂层检测344
第9章 热喷涂346
9.1 热喷涂定义、分类及特点346
9.1.1 热喷涂定义346
9.1.2 热喷涂分类346
9.1.3 热喷涂特点347
9.2 热喷涂原理、工艺及应用347
9.2.1 热喷涂原理及工艺347
9.2.2 热喷涂应用348
9.3 氧-乙炔火焰喷涂349
9.3.1 喷涂与喷熔原理及特点349
9.3.2 重熔351
9.3.3 喷涂与喷熔设备352
9.3.4 喷涂用金属线材355
9.3.5 喷涂(熔)用金属粉末359
9.3.6 喷涂用非金属粉末361
9.3.7 喷涂用复合材料370
9.3.8 金属线材火焰喷涂工艺373
9.3.9 金属粉末火焰喷涂工艺381
9.3.10 火焰喷熔工艺382
9.3.11 火焰喷塑382
9.3.12 火焰喷塑与流化床法、静电喷塑比较385
9.4 超音速火焰喷涂及爆炸火焰喷涂391
9.4.1 超音速火焰喷涂原理391
9.4.2 超音速火焰喷涂设备种类及涂层性能392
9.4.3 爆炸火焰喷涂原理394
9.4.4 爆炸火焰喷涂特点及应用395
9.5 电弧喷涂及线爆喷涂396
9.5.1 电弧喷涂原理396
9.5.2 电弧喷涂特点及应用396
9.5.3 电弧喷涂设备398
9.5.4 电弧喷涂工艺399
9.5.5 线爆喷涂400
9.6 等离子喷涂401
9.6.1 等离子喷涂原理及特点401
9.6.2 等离子喷涂设备402
9.6.3 等离子喷涂工艺403
9.6.4 等离子弧粉末堆焊405
9.7 软线喷涂406
9.7.1 原理406
9.7.2 特点406
9.7.3 应用406
9.8 涂层性能检测406
9.8.1 工艺性能检测406
9.8.2 物理及化学性能检测408
9.9 防腐蚀涂层408
9.9.1 大型钢结构金属喷涂长效防腐408
9.9.2 电弧喷涂防腐411
9.9.3 实用工艺举例414
9.10 防磨损涂层416
9.10.1 模具喷熔修复416
9.10.2 曲轴氧-乙炔火焰线材喷涂修复工艺416
9.10.3 实用工艺举例417
9.11 特殊功能层及其他应用419
9.11.1 聚四氟基体锌铜复合涂层419
9.11.2 实用工艺举例421
9.12 热喷涂单位简介421
9.12.1 北京工达普瑞表面科技发展有限责任公司421
9.12.2 北京新迪表面技术工程有限公司422
第10章 涂料与涂装424
10.1 涂料组成424
10.1.1 成膜物质424
10.1.2 溶剂425
10.1.3 助剂426
10.1.4 颜料426
10.2 涂料的分类427
10.2.1 涂料分类原则427
10.2.2 涂料基础产品简介427
10.3 涂料的性质428
10.3.1 油脂涂料428
10.3.2 天然树脂涂料428
10.3.3 酚醛树脂涂料429
10.3.4 沥青涂料430
10.3.5 醇酸树脂涂料431
10.3.6 氨基树脂涂料432
10.3.7 硝基涂料433
10.3.8 乙烯树脂涂料433
10.3.9 丙烯酸树脂涂料434
10.3.10 聚酯树脂涂料436
10.3.11 环氧树脂涂料436
10.3.12 聚氨酯涂料437
10.3.13 常用涂料举例438
10.4 工件涂装前表面预处理446
10.4.1 钢铁表面预处理446
10.4.2 木材表面预处理448
10.4.3 塑料表面预处理449
10.5 涂装工艺450
10.5.1 涂装工艺分类450
10.5.2 高压无气喷涂451
10.5.3 电泳451
10.5.4 静电喷漆453
10.5.5 静电喷粉455
10.6 埋地钢质管道防腐457
10.6.1 一般规定457
10.6.2 环氧煤沥青防腐层457
10.7 输水管道水泥砂浆衬里457
10.7.1 材料458
10.7.2 衬里前的准备工作458
10.7.3 衬里工艺458
10.7.4 衬里质量检验458
10.7.5 修补460
10.8 砖板衬里460
10.8.1 概述460
10.8.2 耐腐蚀胶泥460
10.8.3 耐腐蚀砖板469
10.8.4 衬里结构473
10.8.5 砖板衬里施工477
10.8.6 质量控制与安全技术479
10.9 涂料和漆膜的质量检验480
10.9.1 涂料外观480
10.9.2 黏度480
10.9.3 漆膜厚度480
10.9.4 漆膜外观481
10.9.5 漆膜附着力测定法481
10.9.6 漆膜冲击试验测定法481
10.9.7 漆膜耐霉菌测定法481
10.9.8 测定耐湿热、耐盐雾、耐候性(人工加速)的漆膜制备法481
10.9.9 漆膜耐盐雾测定法481
10.9.10 漆膜耐湿热测定法482
10.9.11 漆膜老化(人工加速)测定法482
10.9.12 漆膜柔韧性测定法482
10.9.13 漆膜耐水性测定法482
10.9.14 漆膜耐汽油性测定法482
10.9.15 防锈油脂湿热试验法482
10.9.16 色漆和清漆耐湿性的测定482
10.9.17 漆膜硬度测定法482
10.10 漆膜一般制备法482
10.11 涂装作业安全规程482
10.11.1 喷漆室安全技术规定482
10.11.2 涂装作业安全规程482
10.12 热反射隔热防腐降温涂料482
10.12.1 国内外发展状况简述483
10.12.2 热反射隔热防腐蚀涂料设计原则484
10.12.3 APTH的制备485
10.12.4 涂料降温性能检测486
10.12.5 应用487
10.12.6 典型涂料举例487
第11章 化学热处理490
11.1 渗碳490
11.1.1 概述490
11.1.2 渗碳原理491
11.1.3 渗碳层质量的影响因素491
11.1.4 气体渗碳492
11.1.5 液体渗碳502
11.1.6 固体渗碳503
11.1.7 其他渗碳方法505
11.1.8 渗碳用钢及渗碳后的热处理508
11.1.9 渗碳层的组织与性能509
11.1.10 渗碳件的质量检验、常见缺陷及防止措施509
11.2 渗氮511
11.2.1 概述511
11.2.2 渗氮过程及渗氮层组织512
11.2.3 渗氮用钢及渗氮前的热处理514
11.2.4 气体渗氮516
11.2.5 离子渗氮520
11.2.6 渗氮层的组织与性能523
11.2.7 渗氮件的质量检验、常见缺陷及防止措施524
11.2.8 其他渗氮方法527
11.3 钢的碳氮共渗528
11.3.1 概述528
11.3.2 气体碳氮共渗529
11.3.3 液体碳氮共渗531
11.3.4 碳氮共渗后的热处理及渗层组织533
11.3.5 碳氮共渗层的性能534
11.3.6 碳氮共渗件的质量检验、常见缺陷及防止措施535
11.3.7 氮碳共渗536
11.4 渗硼542
11.4.1 固体渗硼542
11.4.2 熔盐渗硼545
11.4.3 其他渗硼方法546
11.4.4 渗硼层的组织与性能547
11.4.5 渗硼材料549
11.4.6 稀土元素的催渗作用550
11.4.7 部分国内厂家开发的商用渗硼剂550
11.5 渗铝550
11.5.1 渗铝的方法及工艺550
11.5.2 渗铝层的组织与性能555
11.6 渗铬557
11.6.1 渗铬的方法及工艺557
11.6.2 渗铬层的组织与性能559
11.7 渗硫、硫氮共渗、硫碳氮共渗561
11.7.1 渗硫561
11.7.2 硫氮共渗及硫碳氮共渗563
11.8 渗硅566
11.8.1 渗硅的方法及工艺567
11.8.2 渗硅层的组织568
11.9 渗锌568
11.9.1 渗锌的方法及工艺568
11.9.2 渗锌层的组织569
11.10 渗其他金属569
11.11 复合渗571
11.11.1 硼铝共渗571
11.11.2 硼硅共渗571
11.11.3 硼铬共渗572
11.11.4 铝硅共渗573
11.11.5 铬铝共渗573
11.12 化学热处理的新进展573
11.12.1 等离子渗碳技术573
11.12.2 热处理对Incone1600合金表面偏聚的影响574
11.12.3 提高模具使用寿命的表面强化新技术574
11.12.4 H13热作模具钢的表面热处理575
11.12.5 机械能助渗铝575
11.12.6 模具热处理工艺577
11.12.7 塑料模具的表面强化技术578
11.12.8 钛合金Ti-6Al-4V的磨损失效及其表面耐磨处理技术579
11.12.9 低碳钢渗铝加离子渗氮的表面硬化处理580
11.12.10 1Cr18Ni9Ti不锈钢的化学热处理工艺581
第12章 堆焊584
12.1 概述584
12.1.1 金属表面堆焊的特点584
12.1.2 堆焊的应用领域584
12.2 堆焊合金的类型及性能585
12.3 堆焊方法587
12.3.1 堆焊方法及工艺587
12.3.2 堆焊方法的选择592
12.4 堆焊材料593
12.4.1 堆焊焊条593
12.4.2 焊丝597
12.4.3 焊剂604
12.4.4 其他堆焊材料606
12.4.5 耐磨堆焊复合钢板607
12.4.6 堆焊材料的选择608
12.5 堆焊检验609
12.5.1 外观检验609
12.5.2 无损检验609
12.5.3 堆焊层的力学性能检验609
12.5.4 堆焊层的耐磨试验609
第13章 物理气相沉积614
13.1 真空技术基础614
13.1.1 真空物理基础614
13.1.2 真空的获得618
13.1.3 真空的测量620
13.2 真空蒸镀624
13.2.1 真空蒸镀原理624
13.2.2 真空蒸发镀膜设备627
13.2.3 真空蒸镀工艺及应用640
13.3 溅射镀膜645
13.3.1 溅射镀膜原理645
13.3.2 溅射镀膜设备656
13.3.3 溅射镀膜工艺及应用661
13.4 离子镀664
13.4.1 离子镀原理664
13.4.2 离子镀设备669
13.4.3 离子镀膜工艺及应用674
13.5 镀膜前处理及膜厚测量681
13.5.1 镀膜前处理681
13.5.2 膜厚测量685
13.6 薄膜的分析测试技术689
13.6.1 薄膜的成分、组织和结构分析689
13.6.2 薄膜的性能测试691
13.7 PVD技术新进展695
13.7.1 方法及设备研究进展695
13.7.2 工艺研究进展698
第14章 离子注入699
14.1 概述699
14.1.1 离子注入技术的发展699
14.1.2 离子注入的特点699
14.1.3 离子注入的局限性700
14.2 离子注入的物理过程701
14.2.1 非晶靶注入离子的射程分布701
14.2.2 离子注入单晶靶中的射程分布706
14.2.3 离子注入元素的分布710
14.2.4 能量淀积分布与注入辐射损伤711
14.3 离子注入装置716
14.3.1 概述716
14.3.2 离子注入机的种类717
14.3.3 离子源723
14.3.4 离子束的加速726
14.3.5 质量分析器727
14.3.6 离子束的偏转、扫描和聚焦727
14.3.7 离子注入剂量728
14.3.8 靶室系统729
14.3.9 真空系统730
14.4 离子注入在半导体技术中的应用732
14.4.1 离子注入在双极器件中的应用732
14.4.2 离子注入在MOS电路中的应用736
14.5 离子注入功能材料740
14.5.1 半导体材料的离子注入740
14.5.2 半导体材料离子注入的工艺特点741
14.5.3 化合物半导体离子注入的特点741
14.5.4 化合物半导体和注入离子种类741
14.5.5 磁性材料的离子注入744
14.5.6 离子注入在超导材料中的应用745
14.6 离子注入与材料表面改性746
14.6.1 离子束与材料的相互作用746
14.6.2 金属材料离子注入改性747
14.6.3 离子注入改善金属材料力学性能748
14.7 离子注入与金属化合物化学效应755
14.7.1 荷能离子与衬底原子的化合755
14.7.2 离子注入与抗化学腐蚀755
14.7.3 离子注入与金属抗氧化性能758
14.8 离子注入辐射损伤与金属相变758
14.8.1 金属离子注入奥氏体钢和相变758
14.8.2 铁素体钢照射组织相变762
14.8.3 氧化物弥散强化钢的组织变化762
14.8.4 离子注入照射材料的近表组织损伤763
14.8.5 金属基复合材料注入损伤764
14.8.6 离子注入辐射相变766
14.8.7 离子注入金属间化合物与合金相767
14.9 离子注入测量技术769
14.9.1 二次离子质谱技术(SIMS)770
14.9.2 核反应分析法(NRA)770
14.9.3 背散射能谱技术(RBS)771
14.9.4 俄歇电子能谱分析(AES)772
14.9.5 正电子湮没技术(PAT)772
14.10 离子注入工艺及其他773
14.10.1 离子注入工艺要求773
14.10.2 离子束混合774
14.10.3 离子束缝合775
14.10.4 离子束反冲注入776
14.10.5 等离子源离子注入777
14.10.6 离子束注入的安全与防护778
14.11 离子注入表面改性技术新进展783
14.11.1 聚合物材料的离子束表面改性及工程应用前景783
14.11.2 原子核物理中的辐照技术784
14.11.3 采用双层辉光离子渗金属技术785
14.11.4 金属材料的离子注入785
14.11.5 离子注入使人工心脏瓣膜表面改性785
14.11.6 氮离子注入材料表面改性技术研究785
14.11.7 GaN材料中离子注入的研究进展786
14.11.8 高速钢刀具离子注入表面改性研究786
14.11.9 等离子体浸没离子注入786
14.11.10 功率元件采用的晶圆日益薄型化786
14.11.11 研究复合表面技术传统的表面技术786
14.11.12 用于半导体材料掺杂787
14.11.13 金属工业离子注入机787
14.11.14 MEVVA源离子注入材料表面改性787
14.11.15 离子注入生物效应788
14.11.16 离子注入制备N型欧姆接触工艺788
第15章 化学气相沉积790
15.1 化学气相沉积通论790
15.1.1 化学气相沉积定义790
15.1.2 化学气相沉积的种类和应用791
15.1.3 化学气相沉积(CVD)的特点及与其他涂层工艺技术的比较793
15.2 化学气相沉积原理794
15.2.1 化学气相沉积一般原理及过程分析794
15.2.2 几种先进的化学气相沉积技术原理简介800
15.3 化学气相沉积工艺与技术806
15.3.1 化学气相沉积技术806
15.3.2 化学气相沉积涂层810
15.4 化学气相沉积的工业应用845
15.4.1 工具钢用CVD法涂覆TiC846
15.4.2 单层涂覆和多层涂覆技术的应用848
第16章 其他方法851
16.1 热烫印851
16.1.1 热烫印原理851
16.1.2 热烫印设备852
16.1.3 热烫印工艺854
16.1.4 热烫印质量855
16.2 冲击镀856
16.2.1 冲击镀原理856
16.2.2 冲击镀锌856
16.2.3 冲击镀锡857
16.2.4 冲击镀镉-锡-铅合金858
16.3 超硬膜技术858
16.3.1 金刚石薄膜858
16.3.2 立方氮化硼860
16.4 激光表面处理861
16.4.1 概述861
16.4.2 激光表面处理装备861
16.4.3 激光表面处理工艺原理861
16.4.4 激光表面处理前的表面预处理862
16.4.5 激光相变硬化863
16.4.6 激光熔凝处理868
16.4.7 激光表面合金化和激光涂敷868
16.4.8 激光冲击强化870
第17章 涂层性能及检测872
17.1 涂层的外观检验872
17.1.1 涂层表面缺陷的检验873
17.1.2 涂层表面粗糙度的检验874
17.1.3 涂层表面光泽度的检验880
17.2 涂层的厚度检验883
17.2.1 测厚方法概述883
17.2.2 测厚方法883
17.3 涂层的耐蚀性检验905
17.3.1 大气暴露试验906
17.3.2 盐雾试验911
17.3.3 铜加速乙酸盐雾试验(CASS法)917
17.3.4 湿热试验919
17.3.5 腐蚀膏试验920
17.3.6 二氧化硫工业气体腐蚀试验921
17.3.7 周期浸润腐蚀试验923
17.3.8 电解腐蚀试验924
17.3.9 其他人工加速腐蚀试验926
17.3.10 涂层耐蚀性检验的国家标准927
17.3.11 输油管道的腐蚀927
17.4 涂层的孔隙率及检验928
17.4.1 涂层孔隙率928
17.4.2 涂层孔隙率测定法928
17.4.3 几种涂层孔隙率的试验方法932
17.5 涂层的结合力及检验936
17.5.1 涂层结合力936
17.5.2 涂层结合力的检验937
17.5.3 几种涂层结合力的检验方法943
17.5.4 有关涂层结合强度试验的国家标准目录959
17.6 涂层的硬度及检验960
17.6.1 几种涂层的硬度960
17.6.2 涂层硬度的特性962
17.6.3 涂层的宏观硬度检验963
17.6.4 涂层的显微硬度检验964
17.6.5 几种涂层硬度的检验方法965
17.6.6 有关涂层硬度试验的国家标准目录974
17.7 涂层的其他性能及检验974
17.7.1 涂层的内应力及检验974
17.7.2 涂层的耐磨性及检验976
17.7.3 涂层的热性能及检验978
17.7.4 几种涂层其他性能的试验方法981
17.7.5 有关涂层其他性能试验的国家标准目录991
主要参考文献993
热门推荐
- 785198.html
- 1385939.html
- 2715297.html
- 712519.html
- 2092232.html
- 3153727.html
- 3132246.html
- 3658098.html
- 3158914.html
- 2145491.html
- http://www.ickdjs.cc/book_381772.html
- http://www.ickdjs.cc/book_3289815.html
- http://www.ickdjs.cc/book_764179.html
- http://www.ickdjs.cc/book_1959921.html
- http://www.ickdjs.cc/book_188724.html
- http://www.ickdjs.cc/book_991805.html
- http://www.ickdjs.cc/book_3004241.html
- http://www.ickdjs.cc/book_1986283.html
- http://www.ickdjs.cc/book_852241.html
- http://www.ickdjs.cc/book_3157594.html